Die großen westlichen Automobilhersteller werden seit geraumer Zeit vom Kapitalmarkt nur noch sehr niedrig bewertet… Volkswagen aktuell (je nach Tag und aktuellem Sentiment bzw. Trump-Faktor) mit einer Marktbewertung i.H.v. ~45 bis 50 Mrd. EUR.
Die Ursache ist relativ klar: Die neuen chinesischen All-Electric OEMs (BYD, XPEng, Nio, Xiaomi etc.) sind dabei technologisch und vor allem preislich an den alteingesessenen Herstellern vorbeizuziehen… und zwar nicht nur in China.
Diese “Bedrohung” durch die chinesischen All-Electric OEMs haben vermutlich nur wenige Marktbeobachter in der Intensität und Geschwindigkeit kommen sehen.
In diesem Artikel möchte ich einmal auf die wesentlichen Wettbewerbsvorteile der chinesischen OEMs eingehen… und darauf, was das für einen Hersteller wie Volkswagen in puncto Marktanteil und Absatzmenge bedeuten könnte.
Der Volkswagen-Konzern (Marken VW, Audi und Skoda) war historisch gesehen mit einem Marktanteil von round about 20% stets der größte OEM auf dem chinesischen Markt (jedenfalls über die letzten zwei Dekaden). Der Marktangang funktionierte dabei größtenteils über die Anfang der 2000er Jahre gegründeten Gemeinschaftsunternehmen (Joint Ventures) mit den lokalen und in Staatseigentum befindlichen OEMs SAIC und FAW, teilweise aber auch über Importe. Inzwischen betreibt Volkswagen in Anhui auch ein Werk, welches sich mehrheitlich (zu 75%) im Besitz der Volkswagen AG befindet und daher vollkonsolidiert in den Jahresabschluss einfließt.
Exporte von in China produzierten Verbrennern fanden aufgrund der nicht vergleichbaren Qualität über den gesamten Zeitraum i.W. nicht statt. D.h. Volkswagen (und andere internationale OEMs) stellten das Know-How zur Verfügung und die JVs konzentrierten sich mit ihren Verbrennungsmotoren i.W. auf den Heimatmarkt.
Mit dem Aufkommen der BEVs (Battery Electric Vehicles) und der chinesischen All-Electric OEMs (BYD etc.) hat sich dieses Bild in den letzten 2-3 Jahren vollständig gewandelt:
- Bereits heute erreichen die batterieelektrischen Fahrzeuge bei den Neuwagenverkäufen in China einen Marktanteil von mehr als 50%, was das Land weltweit zum führenden Markt („Leitmarkt“) in Bezug auf die Elektrifizierung der Pkw-Flotte macht (der chinesische 5-Jahres-Plan hatte die Erreichung dieses Ziels übrigens erst für das Ende der Dekade vorgesehen). Zum Vergleich: In Europa liegt der BEV-Anteil aktuell nur bei knapp über 10%
- Im europäischen Markt machen chinesische OEMs inzwischen bereits ca. 20-25% der neu zugelassenen BEVs aus, d.h. BYD & Co. exportieren inzwischen fast 400.000 Elektrofahrzeuge pro Jahr aus China in die Europäische Union. Und das, obwohl sie noch nicht über ausgebaute Händlernetzwerke verfügen
Dabei ist der hohe BEV-Marktanteil vor allem auf die bereits heute vergleichsweise günstigen Preise von Elektrofahrzeugen in China zurückzuführen (im Jahr 2024 ca. 5% Preisvorteil ggü. einem vergleichbaren Verbrennermodell):
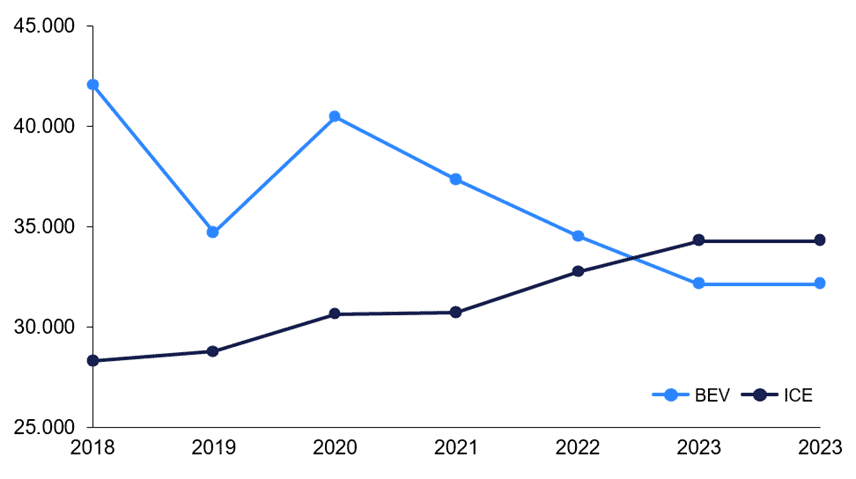
In Europa agieren BYD und Co. eher opportunistisch und passen ihre Preise größtenteils dem europäischen Niveau an bzw. legen sich knapp darunter. Kostenseitig haben die chinesischen All-Electric OEMs (und auch Tesla) aktuell mutmaßlich noch einen substanziellen Vorteil.
Gehen wir einmal auf die wesentlichen Technologie- und Kostenvorteile von Tesla und der chinesischen All-Electric OEMs ein.
Wettbewerbsvorteile der chinesischen All-Electric OEMs
Es ist inzwischen eine industrieweit anerkannte Tatsache, dass sowohl Tesla als auch die chinesischen All-Electric OEMs bestimmte Dinge anders bzw. besser machen als der globale Wettbewerb (was ja zugegebenermaßen durch die Umstellung zum BEV erst ermöglicht wurde).
Stand heute haben sich die chinesischen All-Electric OEMs in mehreren wesentlichen Bereichen einen Vorsprung herausgearbeitet (den die traditionellen OEMs inklusive der Volkswagen AG erst noch aufholen müssen). Dieser Vorsprung basiert insbesondere auf:
- einem für ein Elektrofahrzeug optimierten und skalierbaren Design (Fahrzeugarchitektur und Software-Stack)
- einem teilweise exzessivem Fokus auf Kosteneffizienz (Design-to-Cost Ansatz)
- einer im Vergleich sehr hohen Wertschöpfungstiefe (Produktion von Batteriezellen und -packs sowie E-Motoren etc. inhouse) sowie einem lokal kostenoptimierten Sourcing von Teilen und Komponenten inklusive eines optimierten Rohstoffeinkaufs (Stichwort vertikale Integration)
- niedrigen lokalen Arbeitskosten
- Skalenvorteilen durch den bereits erfolgten Ramp-Up der Produktion (BYD hat bereits einen reinen BEV-Absatz von ca. 1,8 Mio. Fahrzeugen und expandiert gerade global)
Darüber hinaus profitieren die chinesischen All-Electric OEMs von einer ganzen Reihe an staatlichen Subventionen, die – laut EU-Wettbewerbskommission – einen Vorteil i.H.v. 15-20% vom Gesamtumsatz ausmachen können (für einzelne OEMs sogar noch mehr).
Und… nicht zu vergessen: Die Qualität der Fahrzeuge ist durchaus mit der eines deutschen Fahrzeugs vergleichbar. In mancherlei Hinsicht (Fahrgefühl, „Experience“) sind die chinesischen BEVs sogar inzwischen weiter vorne, wie z.B. auch deutsche Nutzer bestätigen:
Wie ist es möglich, dass ein so junges chinesisches Unternehmen die Deutschen Konkurrenten in fast allen Belangen (Reichweite, Ladezeiten, Ausstattung, Verarbeitung, Haptik, Software, Garantiezeiten…) DEUTLICH hinter sich lässt und dann noch 30-50% günstiger angeboten wird? – Alex Graf (Kassenzone Podcast) auf LinkedIn nachdem er einen XPeng getestet hat
Laut der Aussage des CEO von BYD, Wang Chuanfu, sind die Chinesen den traditionellen OEMs bei der Entwicklung der BEVs um ca. 3-5 Jahre voraus:
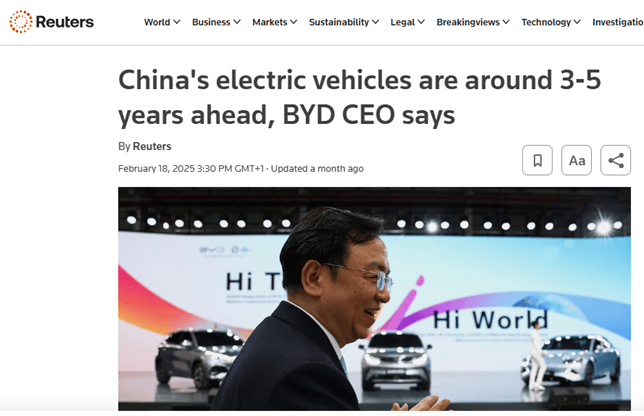
Gehen wir also einmal etwas detaillierter auf die einzelnen Punkte ein… wobei wir dabei nicht vergessen sollten, dass vieles auch eng miteinander zusammenhängt.
Fahrzeug-Architektur und Software
Autokäufer schätzen typischerweise eine gewisse Vielfalt. Gerade wenn es wie bei Volkswagen um den Absatz von mehr als 9 Mio. Fahrzeugen geht, muss der OEM im Grunde für jeden Geschmack ein passendes Angebot parat haben (was Design, Motorisierung und auch Features angeht).
Für den OEM ist diese Produktvielfalt hingegen teuer. Jede Entwicklung kostet Zeit und Geld. Daher versuchen die OEMs gewisse Fahrzeugkomponenten über alle Modelle hinweg einheitlich auszugestalten und damit auch positive Skaleneffekte gegenüber den kleineren Herstellern zu generieren.
Eine solche einheitliche Plattform bzw. ein solcher einheitlicher Baukasten berücksichtigt typischerweise die folgenden Bauteile (Quelle: mobile.de):
- Chassis: Bestimmte Abstände sind festgelegt und können (jedenfalls innerhalb einer Modell-Generation) nicht verändert werden (z.B. der Abstand zwischen Radmitte der Vorderachse und A-Säule, die Neigung des Motors oder die Position und Größe der Batterie)
- Motoren unterscheiden sich in vielen Fällen nur in den Abmessungen und werden in verschiedene Fahrzeuge eingebaut (bei Polo und Passat ist beispielsweise lediglich die Software unterschiedlich)
- Antrieb: Schaltgetriebe bzw. Automatikgetriebe oder Bremsanlage sind stark vereinheitlicht
- Infotainment-Systeme: Infotainment-Systeme sind in vielen Fällen komplett identisch. Der Zugang zu bestimmten Komponenten (z.B. Navi, AppleCar) wird ausschließlich über die Software gesteuert
Irgendwo muss der OEM aber immer auch einen Kompromiss eingehen. Eine Kombination von Verbrenner- und BEV-Baukästen – was die großen OEMs anfangs versucht hatten – hat sich als zu ineffizient für beide Technologien herausgestellt (Batterie und Verbrennungsmotor nehmen zu viel Platz weg, die Anforderungen an die Verkabelung etc. sind diametral unterschiedlich etc.).
Daher: Trotz höherer Anfangsinvestitionen – in Form von Ingenieurstunden, neuen Werkzeugen usw. – zeigen sich die Vorteile von „nativen“ EV-Plattformen gegenüber integrierten Ansätzen inzwischen sehr deutlich… weshalb mittlerweile im Grunde genommen alle großen OEMs mit neuen „BEV only“-Plattformen arbeiten bzw. auf diese umstellen (genau dieser Umstand – das ursprüngliche Engineering von E-Autos auf Basis bestehender Verbrennerplattformen – hat die etablierten OEMs stark zurückgeworfen).
VW nutzt aktuell den modularen Elektrobaukasten (MEB) sowie die Premium Platform Electric (PPE). Die nächste Plattform-Generation, die Scalable Systems Platform (SSP), soll ab 2028 in den ersten Fahrzeugen zum Einsatz kommen.
Was sind also die Vorteile der Nutzung einer nativen BEV-Plattform und aus welchem Grund könnte es ggf. noch Jahre dauern, bis VW und Co. ihren Rückstand wieder wettgemacht haben?
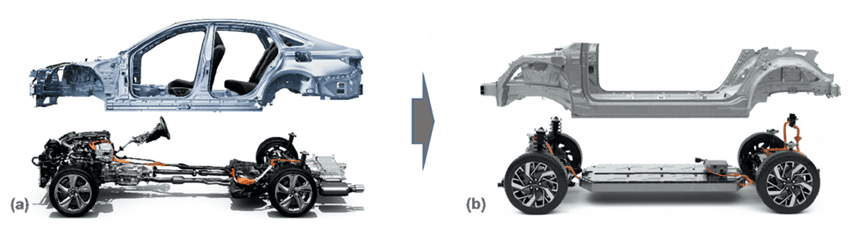
Die Fahrzeugarchitektur vollständig auf ein EV-Konzept auszurichten, ohne nach wie vor veraltete Elemente von Verbrennungsmotoren berücksichtigen zu müssen, bedeutet im Durchschnitt wie gesagt weniger Kompromisse und mehr Flexibilität insbesondere im Hinblick auf Architektur und Rohbau (vgl. hierzu auch den Insights from Vehicle Teardown-Artikel von McKinsey aus 2019):
- Es kann ein größeres Battery Pack integriert und damit eine größere Reichweite erzielt werden (weil keine Integration des Akkupacks in bestehende Strukturen)
- Der EV-Antriebsstrang kann weiter integriert und große Teile der Leistungselektronik in einer geringen Anzahl an Modulen zusammengefasst werden (Beispiel Kabelstrang: Hier gibt es heute integrierte und gewichtsreduzierende Konzepte für die Verbindung von Batterie, E-Motor, Leistungselektonik und Wärmemanagement). Darüber hinaus können einfachere und effizientere Wärmemanagement-Lösungen zum Einsatz kommen (ggf. ohne jegliche Schnittstellen)
- Die elektronische Steuerungsarchitektur kann zentralisiert werden (dann nur noch ca. 3-4 Zentralrechner im Fahrzeug), was die Softwareentwicklung signifikant erleichtert, einfachere Over-the-Air Updates ermöglicht und die Herstellkosten senkt (bessere Effizienz der Verkabelung, stärkere Bündelung, weniger Verbindungen und Protokolle, „leane“ Entwicklung durch weniger Schnittstellen und involvierte Zulieferer / Teams sowie vereinfachte Prozesse)
Die durchschnittlichen Entwicklungs- und Vorinvestitionen für ein neues Fahrzeugmodell liegen bei den traditionellen Automobilherstellern in einer Größenordnung von typischerweise ein bis mehreren Mrd. EUR (je nach Modellsegment). Die Entwicklungszeit beträgt dabei in der Regel etwa vier bis fünf Jahre (genannt wurde für bestimmte VW-Modelle eine Zahl von 52 Monaten).
Im Vergleich dazu konnten die chinesischen All-Electric OEMs ihre Entwicklungsprozesse aufgrund der fortschrittlicheren Architektur bereits erheblich optimieren. Beispielsweise investiert BYD zwar ebenfalls hohe Beträge in die Entwicklung neuer Fahrzeugplattformen bzw. Fahrzeuge (angeblich ca. 100.000 Mitarbeitende im R&D-Bereich), jedoch in einem deutlich verkürzten Zeitrahmen von 18 bis 24 Monaten.
Der technologische Fokus liegt hierbei insbesondere auf der Integration von Batterietechnologien (z.B. durch das eigene Batterieunternehmen FinDreams) und der Entwicklung eigener Softwarelösungen.
The core competitiveness of Chinese EVs comes from mass manufacturing capability, rather than the assembly capabilities. – Liu Xueliang, general manager of BYD Asia-Pacific auto sales division
In puncto Software besteht der Vorteil der chinesischen All-Electric OEMs (und auch von Tesla) im Einsatz der so genannten zonalen Architektur (versus der traditionell eingesetzten Steuerung nach Domänen).
Kurz zur Einordnung:
Bei der Domänenarchitektur im Auto (in der folgenden Darstellung links dargestellt) werden elektronische Steuergeräte (ECUs) nach Funktionen oder “Domänen” gruppiert – zum Beispiel Antrieb, Infotainment, Fahrerassistenz oder Karosserie. Jede Domäne hat dabei ihre eigene leistungsfähige zentrale Recheneinheit, die mit verschiedenen Sensoren und Aktoren innerhalb dieser Funktionseinheit kommuniziert. Diese Struktur ist ein Zwischenschritt auf dem Weg zur Zentralisierung, da sie bereits viele kleinere Steuergeräte innerhalb einer Domäne zusammenfasst, aber noch nicht domänenübergreifend agiert.
Vorteil: Klare funktionale Trennung und bessere Skalierbarkeit innerhalb der jeweiligen Domäne.
Großer Nachteil allerdings: Viele, viele Kabelstränge, die das Fahrzeug schwer machen, sowie sehr komplexe Datenflüsse (heißt viele Schnittstellen) etc.
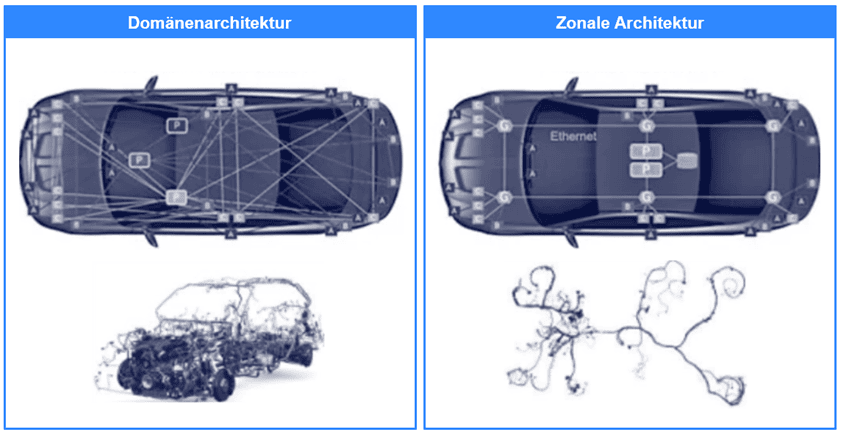
Im Gegensatz dazu basiert die zonale Architektur (in der obigen Darstellung rechts zu sehen) auf der physischen Verteilung im Fahrzeug: Es gibt so genannte Zonen-Controller, die jeweils für einen bestimmten Fahrzeugbereich zuständig sind – z. B. Front links, Heck rechts etc. Diese Controller bündeln alle Daten aus ihrer Zone (egal ob es um Licht, Sensorik oder Sicherheit geht) und leiten sie an eine zentrale Recheneinheit oder ein zentrales Rechensystem weiter.
Der große Vorteil: Weniger Kabel, geringeres Gewicht und eine klarere physikalische Struktur, was vor allem bei der Software- und Update-Architektur moderner Fahrzeuge (Stichwort: Over-the-Air-Updates) Vorteile bringt. Zentrale Rechenleistung wird dabei stärker konsolidiert – ideal für software-definierte Fahrzeuge.
Auch was den Einsatz der zonalen Architektur angeht, war Tesla übrigens Vorreiter. Bereits 2017 wurde beim Model 3 der Kabelbaum deutlich reduziert – laut S&P Global Mobility verschaffte das Tesla einen Entwicklungsvorsprung von grob fünf Jahren. Auch die chinesischen und andere All-Electric OEMs sind allerdings inzwischen soweit: BYD setzt die zonale Architektur seit 2022 in seinen Fahrzeugen ein, Xpeng und Dongfeng seit 2023. Auch der US-Hersteller Rivian setzt auf eine zonale Software-Architektur (in der 2. Generation mit 3 Zonen: East, West und South).
Design-to-Cost-Ansatz: Exzessiver Fokus auf Kosteneffizienz
Eng verknüpft mit den Vorteilen einer optimierten Fahrzeug-Architektur bzw. BEV-Plattform ist das Heben von Verbesserungspotenzialen auf der Kostenseite zu sehen. Sowohl Tesla als auch die chinesischen All-Electric OEMs konnten in den vergangenen Jahren riesige Fortschritte in bezug auf die Optimierung von Herstellungsprozessen und -kosten machen.
Hier ein paar Beispiele für Innovationen von Tesla und BYD:
- Keine 5- bis 6-jährigen Modellzyklen mehr, stattdessen kontinuierliche Verbesserung (z.B. innerhalb von zwei Jahren 8%iger Gewichtsverlust der Rohkarosserie von Model Y, ggü. Ursprungsmodell sogar -60%). Ausrollen neuer innovationen über alle bestehenden Modelle hinweg
- BYD: Einsatz der Blade-Batterie sowohl als Energiespeicher als auch als strukturelles Bauteil. Daher entscheidende Rolle bei der Verbesserung der Fahrzeugstruktur und der Sicherheitsleistung
- Tesla: Einsatz eines neuen eigenentwickelten und energieoptimierten Chips und Inverters. Dadurch bei der Transformation von Hochvolt- auf Niedervoltstrom um 50% reduzierter Energieverbrauch
- Tesla: Einsatz von Dauermagnetmotoren der nächsten Generation ohne den Einsatz seltener Erden (im aktuellen Model Y noch >500g)
- Tesla Cybertruck: Einsatz von 48-Volt-Elektroarchitektur und Gigabit-Ethernet-Loop (“Highspeed-Autobahn” für Daten) und damit Reduktion der Kabelanzahl um 68% sowie des Kabelgewichts um 84% (Hochleistungskabel)
- Tesla / chin. OEMs: Einsatz von „Gigapressen“, d.h. Gießen großer Karosserieteile in einem Stück (und Verzicht auf aufwendige Schraubverbindungen). Einsparpotenzial (laut Toyota-Ingenieuren) bei mehreren hundert Teilen und 100kg Fahrzeuggewicht
- Experimentieren mit alternativen Herstellungsprozessen: Tesla stellt Überlegungen zur Einführung eines alternativen Herstellungsprozesses an („Unboxing“ versus traditionelle Fließbandproduktion), was die Ausgestaltung der Produktionslinien komplett über den Haufen werfen und zu weiteren größeren Einsparungen führen könnte (insbesondere bei der Durchlaufzeit und damit dem möglichen Output einer Fabrik).
Darüber hinaus haben wir natürlich alle noch die damaligen Berichte aus der Tesla-„Produktionshölle“ im Kopf:
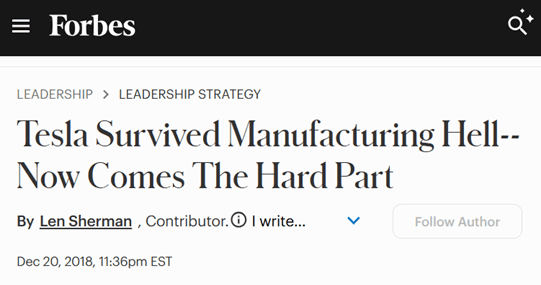
Offenbar hat CEO Elon Musk damals höchstpersönlich in Vollzeit dabei geholfen, die Abläufe im Werk Austin zu optimieren (und sich dabei teilweise auch mit sehr kleinteiligen Prozessen befasst).
Was diese Episode vor allem zeigt: Die Wettbewerber stellen nicht nur quasi alle bisher etablierten Vorgehensweisen in Frage, sondern legen auch einen überdurchschnittlich hohen Ehrgeiz an den Tag (andererseits hat Tesla, wie aktuell überall berichtet, mit einer hohen Mitarbeiterfluktuation zu kämpfen – als Resultat der schlechten Arbeitsbedingungen und Bezahlung).
Hohe Wertschöfpfungstiefe und optimierte Supply Chain
Ein weiterer wichtiger Aspekt ist die Wertschöpfungstiefe. Während traditionelle europäische OEMs wie Volkswagen seit Jahrzehnten stark auf ein globales Zulieferernetzwerk setzen, hat sich in China ein anderer Ansatz etabliert.
Chinesische Hersteller – allen voran BYD – verfolgen ein vertikal integriertes Geschäftsmodell, das ihnen eine deutlich höhere Kontrolle über wesentliche Komponenten ermöglicht. Tesla verfolgt grundsätzlich einen ähnlichen Ansatz.
When you break down [a Chinese BEV] you see that the difference is only in two systems, one is the sourcing of parts – all the parts are sourced locally in China – and second one ist the cost of batteries. Thats what makes the difference and they have this 30% ex-works competitive edge. – Carlos Tavares (Ex-CEO Stellantis)
Die Wertschöpfungstiefe von BYD ist mit über 70% außergewöhnlich hoch, was bedeutet, dass das Unternehmen große Teile der erforderlichen Komponenten inhouse produziert.
Zum Vergleich: Bei Tesla liegt die Wertschöpfungstiefe bei irgendwo knapp unter 50%, bei einem typischen europäischen OEM traditionell unterhalb der 30%-Marke:
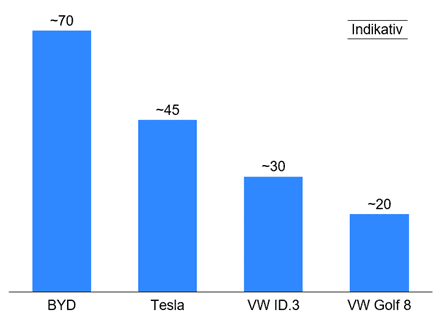
BYD und Tesla produzieren also nicht nur die zu ihren Autos zugehörigen Elektromoten selbst (das macht z.B. VW in Kassel ja auch), sondern gehen was die Integration der Wertschöpfungskette angeht noch einen großen Schritt weiter. U.a. werden die folgenden Vorprodukte bzw. Komponenten intern hergestellt:
- Raffiniertes Lithium (Tesla)
- Batteriezellen und -packs (BYD und Tesla)
- Eigene Chipdesigns (BYD und Tesla)
- Eigene Controller (Tesla)
- Eigene Roboter(-Arme) (BYD)
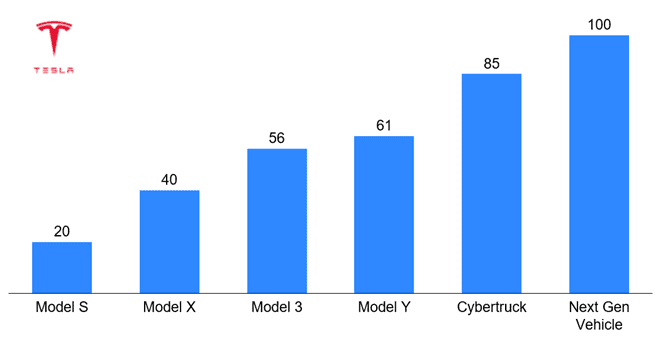
Diese Strategie reduziert nicht nur die Abhängigkeit von externen Lieferanten, sondern führt aufgrund der Relevanz des integrierten Ansatzes bei einem digitalisierten Elektrofahrzeug auch zu erheblichen Kosten- und ggf. auch Innovationsvorteilen.
Beispiel Batterieproduktion:
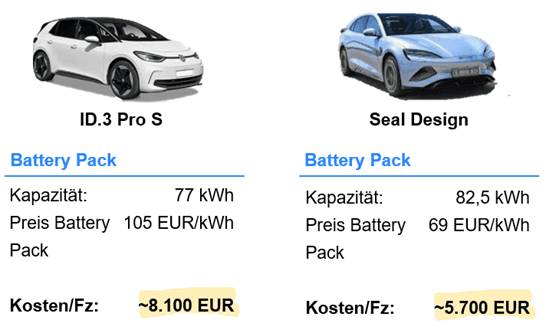
Während BYD im Grunde genommen die Battery Packs zu Selbstkosten von seiner Tochtergesellschaft FinDreams lokal beziehen kann, muss Volkswagen aktuell noch zu Marktpreisen von CATL einkaufen… und CATL berechnet internationeln Kunden entsprechend der Analyse der EU-Kommission substanziell mehr, als lokalen Abnehmern (mehr dazu im Unterkapitel zu den staatlichen Subventionen).
Aufgrund der weltweiten Überkapazitäten haben sich die Batteriepreise in den vergangenen Monaten allerdings bereits stark den Kosten angenähert:
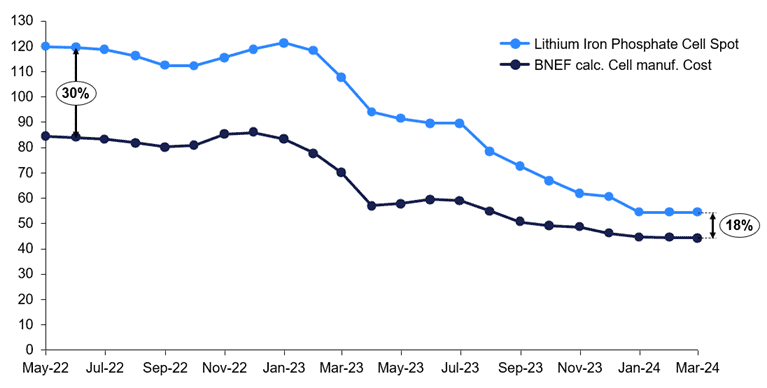
Hinweis: In der obigen Abbildung sind die Preise und Herstellkosten für Batteriezellen abgebildet. Um Preis bzw. Kosten eines Battery Packs zu erhalten, müssen noch ca. 35 bzw. 25 USD / kWh für den Zusammenbau des Packs zu den Zell-Preisen hinzuaddiert werden.
Ein weiterer wichtiger Aspekt: Aufgrund der vertikalen Integration ist ein Player wie BYD ggf. auch innovativer, als ein OEM-unabhängiger Hersteller.
Die neueste BYD-Entwicklung ist beispielsweise eine Batterie, die i.W. genauso schnell aufgeladen werden kann wie der Benzintank eines üblichen Verbrenners (43% Aufladung in 4-5 Minuten möglich):
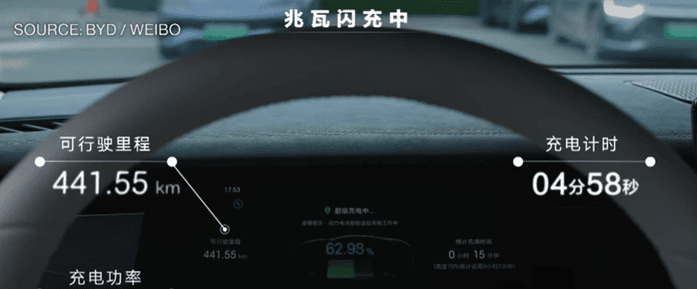
Darüber hinaus können die Batterien von BYD durch das bidirektionale Laden / Entladen auch als genereller Energiespeicher verwendet und als solcher ins übergeordnete Energiesystem eingebunden werden.
Westliche OEMs setzen im Vergleich traditionell zwar auf eine eher arbeitsteilige und fragmentiertere Zulieferkette. Was die Batterieproduktion angeht, ist allerdings mindestens Volkswagen inzwischen auch auf den Weg von BYD und Tesla eingeschwenkt.
Niedrige Arbeitskosten
Aufgrund der niedrigen Arbeitskosten in China haben die chinesischen OEMs logischerweise einen substanziellen Kostenvorteil, der die in Summe immernoch geringere Produktivität im Vergleich zu den europäischen OEMs mehr als ausgleicht.
Bezogen auf ein typisches Elektrofahrzeug kann dieser Kostenvorteil bis zu ca. 1.500 EUR je Fahrzeug betragen:
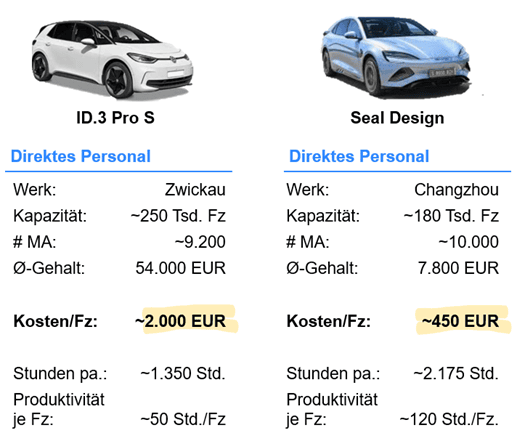
Kurz zur Erläuterung:
- Der RMB / EUR-Wechselkurs wurde mit ~7,7 RMB / EUR entsprechend des heutigen Niveaus angesetzt
- In lokaler Währung wurde das Jahresgehalt eines durchschnittlichen chinesischen Mitarbeiters zu ~60.000 RMB angesetzt
- Das Lohn- und Gehaltsniveau bei VW in Zwickau bewegt sich entsprechend Glassdoor in der Größenordnung von ~55.000 EUR pa
- Die durchschnittliche Jahresarbeitszeit in Deutschland ist mit ca. 1.350 Arbeitsstunden pro Jahr eine der niedrigsten weltweit. Nichts desto trotz ergibt sich im Vergleich für das Werk eine signifikant höhere Personalproduktivität (50 Mannstunden je Fz. versus ~120 Mannstunden je Fz.), was allerdings auch auf Unterschiede in der Fertigungstiefe des Standorts zurückzuführen sein könnte (wenn z.B. BYD in Changzhou noch eine Komponentenfertigung in Betrieb hätte – hierzu habe ich allerdings keine Infos)
- Hier werden wohlgemerkt nur die direkten Arbeitskosten betrachtet. Personalkostenunterschiede in den Bereichen Verwaltung & Vertrieb, Forschung & Entwicklung, Komponenten- und Batterieherstellung etc. sind hier nicht berücksichtigt
Aufgrund der zunehmenden Lokalisierung der Produktion (heißt Fahrzeuge für den chinesischen Markt werden tendenziell in China produziert, Fahrzeuge für den europäischen Markt in Europa etc.) treten solche globalen Kostenvergleiche allerdings etwas in den Hintergrund. Aber auch in einer regionalen Betrachtung gibt es teils signifikante Unterschiede.
Zwei, drei Beispiele:
- BYD: BYD baut aktuell sein erstes europäisches Werk im ungarischen Szeged auf. Die Arbeitskosten in Ungarn liegen aktuell nur bei ca. 30% der Arbeitskosten in Westdeutschland (Wolfsburg, Ingolstadt etc.)
- Tesla USA: Tesla zahlt laut Bloomberg in den USA inkl. Nebenkosten ca. 45 USD je Stunde. Im Vergleich dazu liegen die Arbeitskosten bei den direkten Wettbewerbern GM oder Ford eher bei ca. 65-70 USD je Stunde
- Tesla Germany: In Grünheide bei Berlin hat Tesla laut Schätzungen der IG Metall einen Arbeitskostenvorteil von ca. 20% ggü. VW und Co. (ein Vorteil, den das ID.3-Werk in Zwickau dann allerdings – mit ein paar Abstrichen vielleicht – ebenso haben sollte)
Skalenvorteile durch Massenproduktion
Aufgrund der kapitalintensiven Produktionsprozesse und der grundsätzlich hohen Fixkosten, haben die Player in der Automobilindustrie klassischerweise immer nach Größe gestrebt.
Die Logik dahinter ist ziemlich einfach: Fixkosten, die i.W. volumenunabhängig anfallen, können bei größeren Produktionsmengen auf mehr Fahrzeuge verteilt werden, was die Stückkosten je Fahrzeug entsprechend verringert.
Elon Musk’s Masterplan war es von Beginn an, die Produktionskosten über die Ausweitung der Produktionsmenge soweit zu senken, dass die Fahrzeuge auch für Menschen mit kleinerem Geldbeutel erschwinglich wurden.
Musk‘s „Masterplan“ ist übrigens noch heute auf der Tesla-Webseite abrufbar. Hier die Kurzfassung:
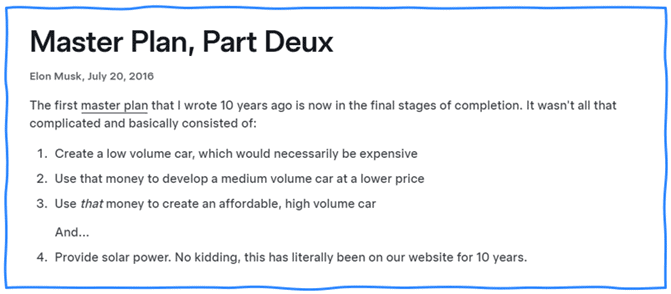
In puncto Elektrofahrzeuge sind BYD und Tesla mit jeweils ca. 1,8 Mio. BEVs pro Jahr aktuell mehr als doppelt so groß wie der Volkswagen-Konzern. (Hinweis: BYD verkauft inkl. der Plugin-Hybride insgesamt bereits ca. 4,2 Mio. Fahrzeuge pa.)
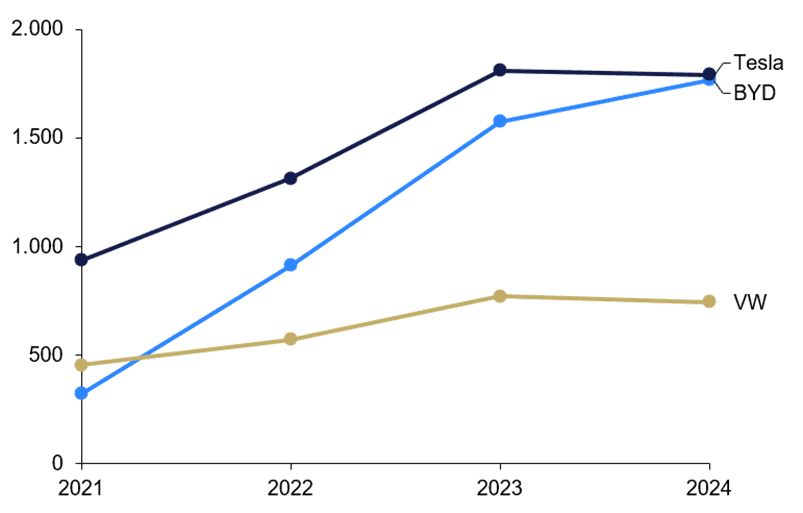
Positive Skaleneffekte sollten also insbesondere aus der Verteilung der Forschungs- und Entwicklungskosten (R&D-Aufwendungen) auf eine größere Grundgesamtheit an Fahrzeugen entstehen sowie ggf. auch auf Werksebene, weil die Fabriken in China ggf. besser ausgelastet sind, als die in Deutschland.
Bzgl. der Umlage anderer Fixkosten auf der „Corporate“- und der regionalen Ebene (übergeordnete Verwaltung bzw. Zentralkosten, regionale Vertriebsorganisationen etc.) sollte allerdings tendenziell die gesamte relevante Fahrzeugproduktion herangezogen werden (also Verbrenner, Hybride und BEVs).
In dieser Hinsicht haben die bereits global agierenden traditionellen OEMs unter Umständen sogar einen gewissen Vorteil… sofern sie „lean“ aufgestellt sind und nicht zu hohe Overhead-Kosten (Gemeinkosten / Zentralkosten) mit sich rumschleppen… ein Punkt mit gewisser Relevanz für einige der großen westlichen OEMs.
Staatliche Subventionen
Zum 30. Oktober 2024 verhängte die EU Strafzölle i.H.v. bis zu 35% auf aus China importierte BEVs verschiedener Hersteller.
Die Höhe der Zölle basiert auf einer Analyse der staatlichen Subventionen für die chinesischen OEMs durch die EU-Wettbewerbskommission.
Laut dieser Analyse erhalten bzw. erhielten die chinesischen All-Electric OEMs Subventionen bzw. staatliche Unterstützung und Erleichterungen in den folgenden Bereichen:
- Bereitstellung vergünstigter Darlehen, Kreditlinien etc.
- Direkte Barzuschüsse und Förderungen („neuartige Antriebstechnik“)
- Bereitstellung von Waren und Dienstleistungen durch staatliche Stellen unter Marktpreis (insbesondere geht es hier um Grund und Boden für den Aufbau von Fabriken sowie Batterien und / oder Lithium für die Batterieproduktion)
- Steuerbefreiungen und Ermäßigungen
Wie der folgenden tabellarischen Aufstellung zu entnehmen ist, scheinen die chinesischen OEMs i.d.R. von mehr als einer „Subventionsquelle“ zu profitieren. Förderungen und Subventionen können dabei sowohl von der Regierung in Peking als auch von der lokalen Provinzregierung gewährt werden.
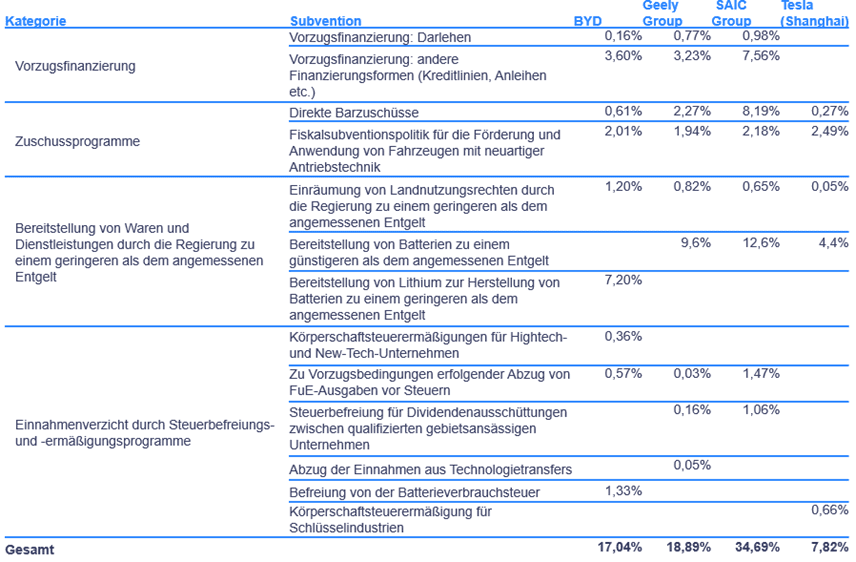
Was auffällt: Die mit Abstand größten Einzelsubventionen beziehen sich auf die Bereitstellung vergünstigter Batterien (bzw. im Fall von BYD Lithium für die Batterieproduktion) und liegen zwischen 4,4 und 12,6%.
Für BYD kam die EU Kommission beispielsweise zu dem Schluss, dass die aggregierte Subventionsquote bei ca. 17% vom Gesamtumsatz liegt und dass subventioniertes Lithium davon ca. 7% ausmacht… das wären in absoluten Zahlen ca. 1.500 EUR je Fahrzeug bzw. Batterie.
Ergebnis: China mit Ex-Works Kostenvorteil von ca. 30-40%
Die chinesischen All-Electric OEMs (z.B. BYD, NIO, XPeng, LeapMotor, Lynk&Co, Xiaomi, Huawei) haben im Vergleich zu den traditionellen westlichen OEMs einen „Greenfield“-Ansatz verfolgt… sowohl was das Engineering, die Softwareentwicklung und den Aufbau der Zulieferkette, als auch die Konzeption der Produktionsstätten angeht.
Hinzu kommt die Vorreiterrolle Chinas bei der Entwicklung von Batteriezellen und -packs, wobei CATL als größter Hersteller weltweit eine zentrale Rolle spielt.
Darüber hinaus profitieren die chinesischen Hersteller von staatlichen Subventionen, insbesondere bei der Land- und Kapitalbeschaffung sowie ggf. der vergünstigten Bereitstellung von Lithium und Batteriezellen.
Alles in allem ergibt sich aus den genannten Faktoren laut der Investment-Bank UBS ein Kostenvorteil für BYD und Co. (Ex-Works) von insgesamt 30-40%, wie die folgende aggregierte Darstellung zeigt:
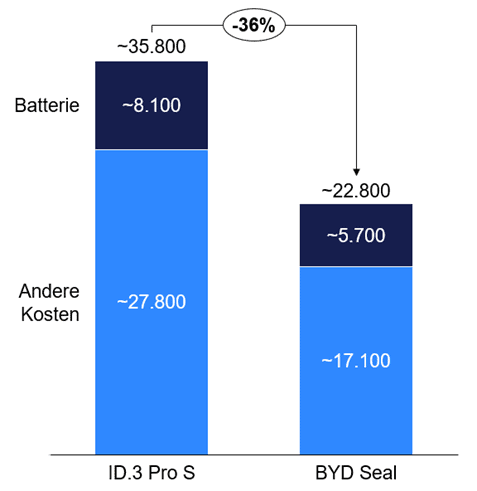
Wesentliche Erkenntnis hieraus: Die chinesischen Hersteller haben Kostenvorteile in allen wesentlichen Kostenkategorien, wobei die inhouse von der Tochtergesellschaft FinDreams entwickelte „Blade“-Batterie von den UBS-Analysten nochmal besonders hervorgehoben wird (hohes Cell-to-Pack-Integrationsverhältnis, einzigartiges Batteriemanagementsystem, die einfache Integration in den Herstellungsprozess, verbesserte Crashsicherheit).
Diese Größenordnung wird auch durch andere Industrieexperten bestätigt: Laut Carlos Tavares (Ex-CEO von Stellantis) liegt der Kostenvorteil gegenüber den europäischen BEV-Herstellern bei ca. 30% und damit auf einem wettbewerbsfähigen Niveau im Vergleich zu den lokalen (heißt chinesischen) Verbrennern.
Was hier allerdings noch dazu gesagt werden muss: Die Fahrzeug-spezifischen Entwicklungskosten (R&D) sind in der Betrachtung nach meinem Dafürhalten nicht enthalten. Das gilt sowohl für die direkt als Aufwand erfassten Forschungs- und Entwicklungskosten als auch für die aktivierten Entwicklungskosten, von denen laut Aussage VW aktuell ca. 70% in die Entwicklung der BEVs fließen.
What’s next? Mögliche Auswirkungen des Kostennachteils
Ein Kostennachteil i.H.v. ~30-40% ist natürlich nicht schön, muss aber aus mehrerlei Hinsicht etwas relativiert werden.
Zum einen reduziert sich der Kostenvorteil nach Berücksichtigung von Logistikkosten, Importzöllen etc. auf etwa 10-15%. Zum anderen sehen wir gerade eine Entwicklung, die auf eine immer stärkere „Regionalisierung“ der Märke hindeutet. Hierfür gibt es drei wesentliche Treiber:
- Die entwickelten (hochpreisigen) Regionen schotten ihre Märkte durch die Einführung von Importzöllen zunehmend ab bzw. haben eine gewisse „Local Content“-Anforderung
- In den Emerging Markets (hierzu würde auch China noch zählen) beobachten wir ein anderes Konsumverhalten und tendenziell eine niedrigere Zahlungsbereitschaft
- Die Ökosysteme der Fahrzeug-Software unterscheiden sich regional sehr stark (insbesondere zwischen China und dem Rest der Welt)
Vereinfacht gesprochen bedeutet das, dass die Fahrzeuge sowie auch die Software aus Wettbewerbsgründen tendenziell dort entwickelt und produziert werden (müssen), wo sich auch die Nachfrage befindet… und zwar in der nachgefragten Qualität und mit den nachgefragten Features (kann auch wieder alternative Technologien beinhalten).
Das heißt mittelfristig wird BYD die Fahrzeuge für den europäischen Markt mutmaßlich in Europa produzieren, wodurch sich die Herstellkosten denen der europäischen Wettbewerber angleichen werden (ein erstes Werk in Ungarn wird aktuell ja bereits aufgebaut). Für Volkswagen und die anderen westlichen OEMs stellt sich hier insbesondere die Frage, ob die Herstellkosten am Standort Deutschland mittel- bis langfristig auf einem wettbewerbsfähigen Niveau gehalten werden können.
Spoiler: Für die besonders kostengünstigen BEVs, den ID.2All und den ID.Every1 kommt ein Produktionsstandort in Deutschland schonmal nicht in Frage. Stattdessen wird sich die Produktion laut VW in Portugal bzw. Spanien befinden (inkl. lokaler Batteriefertigung in Valencia).
Umgekehrt wird Volkswagen seine Modelle für den chinesischen Markt mit lokalen Partnern (XPeng) entwickeln und produzieren… und daher mutmaßlich auch von den lokalen Kostenvorteilen profitieren können.
Europa und Rest der Welt
Was auf Basis der Faktenlage festzustehen scheint: Da die chinesischen All-Electric OEMs in Europa Marktanteile gewinnen wollen, werden vermutlich auch die BEV-Preise in Europa weiter unter Druck bleiben. Aktuell haben sich die chinsischen OEMs bereits einen Marktanteil von ca. 25% am europäischen BEV-Markt gesichert:
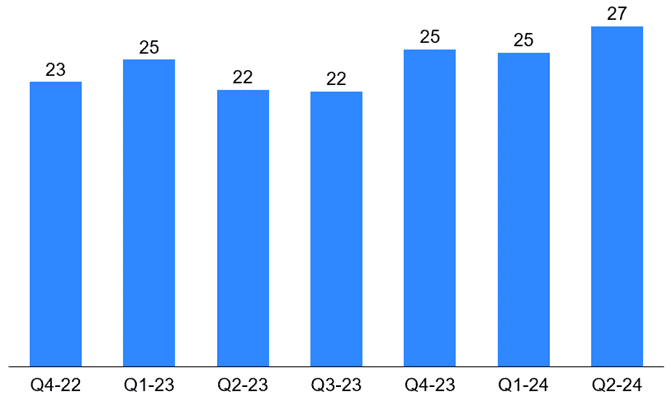
Diese Größenordnung ist in etwa vergleichbar zu dem Anteil, den die japanischen OEMs (Toyota, Nissan, Suzuki, Mazda, Honda, Mitsubishi etc.) in den 1980er Jahren in der Lage waren aufzubauen… übigens mit ähnlichen wettbewerblichen Hürden, wie wir sie heute in Bezug auf die Chinesen beobachten können („Local Content“, Importzölle etc.).
Wenn wir also dieses Szenario einmal etwas weiterdenken, dann könnte die Verteilung der Marktanteile in einem zukünftigen „All-BEV“-Szenario wie folgt aussehen:
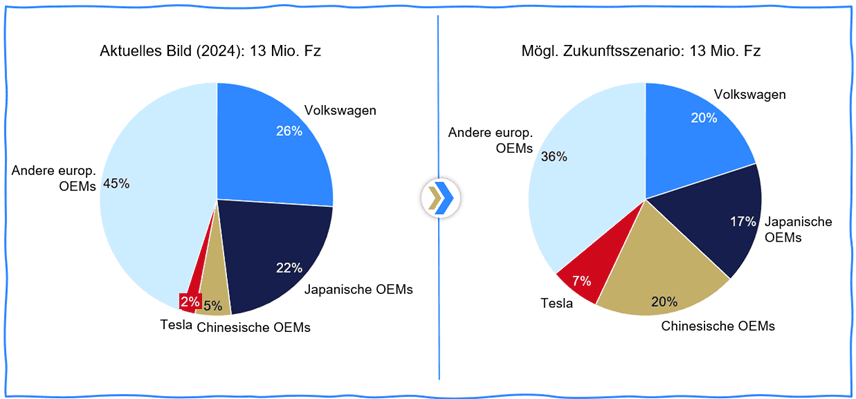
Hinweis: Ich bin hier einmal davon ausgegangen, dass Tesla seine Fabrik in Grünheide wie geplant auf 1 Mio. Fahrzeuge pa ausbaut und diese ausschließlich für den europäischen Markt gedacht sind. Aktuell sieht es allerdings erstmal nicht danach aus, als würde diese Expansion tatsächlich umgesetzt (hoher Widerstand der Bevölkerung, Schwierigkeiten bei der Akquirierung von gutem Personal, weil niedrige Löhne und Gehälter und schlechte Arbeitsbedingungen).
Wie auch immer: Die Materialisierung eines solchen Szenarios würde für Volkswagen eine Marktanteilseinbuße von ca. 5% bedeuten, was bei aktuell ca. 13 Mio. Fahrzeugen einen Verlust von ca. 650 Tsd. Fahrzeugen entsprechen würde. Die Absatzmenge des Volkswagen-Konzerns in Europa würde sich also – bei konstanter Marktgröße – von ca. 3,4 Mio. Fahrzeugen auf ~2,7 Mio. Fahrzeuge verringern.
Global betrachtet könnten die chinesischen OEMs in einigen Regionen (insbes. Südostasien, Mittlerer Osten, Afrika, Russland) sogar weitaus höhere Marktanteile erreichen. Zugegebenermaßen sind die Verkaufszahlen des VW-Konzerns in diesen Region allerdings eher überschaubar (~650-700 Tsd. Fahrzeuge).
China
In China ist die Situation schon seit einiger Zeit etwas angespannter.
Beispiel Volkswagen: Der Nettogewinn der chinesischen JVs sowie auch die an den Volkswagen-Konzern ausbezahlte Dividende ist bereits seit mindestens 10 Jahren auf dem absteigenden Ast… seit 2020 beschleunigte sich der Niedergang jedoch zusehends (ich denke der Corona-Lockdown und die Marktanteilsgewinne von BYD und Co. sind mehr oder weniger fließend ineinander übergegangen).
Im Jahr 2024 betrug der VW-Gewinnanteil nur noch ca. 1,3 Mrd. EUR (versus fast 3,8 Mrd. EUR in 2015):
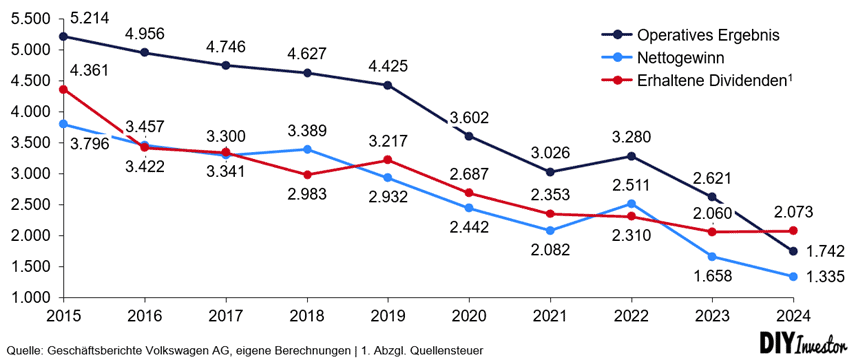
Wenn man mal vom Hochpunkt ausgeht, hat sich der VW-Marktanteil in China über die letzten Jahre um ca. 5%-Punkte verringert (von ~20 auf ~15%):
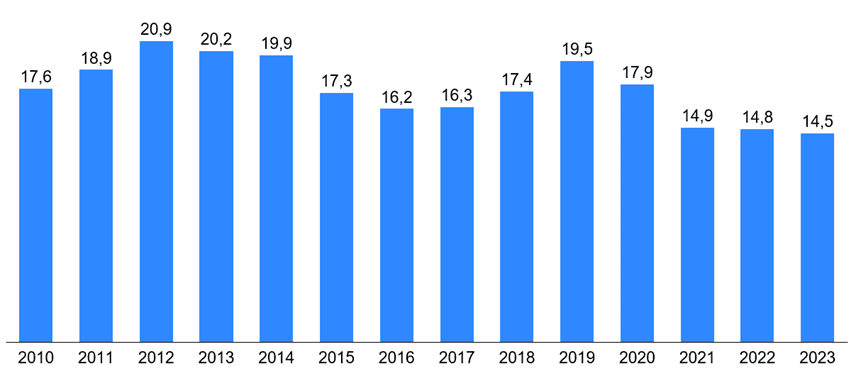
Für das laufende Jahr 2025 geht Volkswagen darüber hinaus von einem nochmal signifikant rückläufigen Ergebnis, konkret einem Abschmelzen des operativen Gewinns um weitere 40-70% aus (also um ca. 700 bis 1.200 Mio. EUR).
Ohne Gegenmaßnahmen, bin ich der Meinung, wird dieser Trend weiter anhalten und das China-Geschäft der westlichen OEMs über die Zeit verschwinden.
Auf die konkreten Gegenmaßnahmen (und deren Erfolgsaussichten) werde ich dann in den kommenden Artikeln etwas detaillierter eingehen. Stay tuned.
1 Gedanke zu „Automobilindustrie: Die historische Bedrohung durch die chinesischen All-Electric OEMs“
Klasse aufbereitet, sehr lesenswert. Vielen Dank und Lg